Plastics Solutions
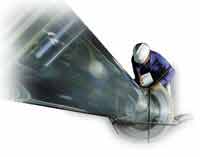
Noncontact Temperature Measurement in
Plastic Industries
VIKING International offers a wide variety of
infrared thermometers that monitor and control
temperature in plastics manufacturing processes.
These thermometers measure temperatures of fast
moving processes quickly and efficiently. They
measure the temperature of the product directly,
instead of the oven or the dryer, allowing you
to quickly adjust process parameters to ensure
top product quality.
VIKING International's infrared thermometers are
easily integrated into existing process control
systems and have the following benefits:
• Non-destructive: the product is never
touched or contaminated.
• Fast and reliable: moving objects are
measured accurately and quickly.
• Flexible: temperature measurements can be
made of a large area or a small spot.
Major Applications
Blown Film Extrusion - Maintain the
plastic's tensile integrity and thickness with
accurate temperature monitoring and the ability
to adjust heating and cooling.
Cast Film Extrusion - Control
temperatures for proper thickness and finish
uniformity with VIKING International infrared
thermometers, and detect potential die bolt
heater problems or plugged dies.
Originally-oriented Film Extrusion -
Mount VIKING International sensors at the cast
roll unit for chill roll control and at the
preheater and cooling units, for heating and
cooling control.
Sheet Extrusion - VIKING International
linescanners allow operators to monitor sheet
temperature and to adjust the die heater for
consistent product quality.
Extrusion Coating - Monitor molten web
within the narrow and often difficult to access
measurement area when using VIKING International
sensors.
Laminating and Embossing - Use an MP50
linescanner to monitor cross-web temperatures
and to help control heating adjustments.
Thermoforming - Ensure proper
temperatures for laminating a multilayer product
for subsequent forming. Monitor the material's
temperature distribution at its proper level
prior to entering the thermoformer.
|